Oil price has been fluctuating since the global economic crises end 2008. However, the oil price in general is stabilizing at about US$ 80 per barrel. This price level is able to drive explorers to drill more wells. Many investors came to me and asked how to develop oil blocks in Indonesia. The most common decision to be made is to acquire a producing block or to apply KSO to Pertamina. KSO is a kind of Joint Operation to develop old fields formerly operated by Pertamina. Pertamina is a state oil company in Indonesia.
When a company has to decide acquiring an oil block, the company has to value the block. Please find a very simple calculation to give you a block value.
1. Assume Oil price per barrel is US$ 80
2. Operating Costs in general in Indonesia say about US$ 20 per barrel
3. Gross Margin should be US$ 80 - US 20 = US$ 60
4. Profit Sharing in Indonesia Government Tax system for KSO is about 10 % net to the partner.
5. Profit Sharing for the companuy is therefore about 10 % x US$ 60 = US$ 6 per barrel.
6. If you make Discounted of the Profit sharing, the Discounted Value should be less than US$ 6.
7. Assume the total discounted value is about 50 % from the cashflow during 20 year contract period than the Net Presenta Value per baerrel is about US$ 3 per barrel remaining reserves
I hope the very rough calculation above could help you estimating the block value during your negotiations.
Dr. Ir. Hasan Hambali
Energy and Environment
Rig
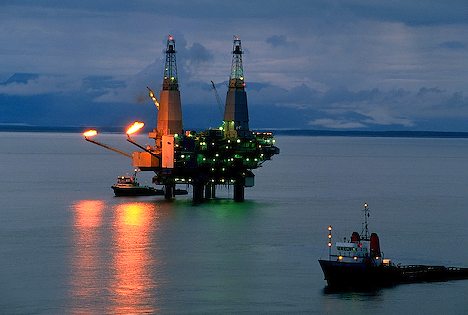
Rig
Tuesday, August 10, 2010
Sunday, August 31, 2008
Surfactant Injection to Increase Recovery Factor
Basic Concept of Surfactant Injection
Surfactant is chemical material which has ability to dissolve oil in water by forming emulsion. Without surfactant, oil is always separated from water and it’s impossible to dissolve. The irreducible oil in the reservoir is trapped and can’t be pushed by water as oil and water has high interfacial tension. Surfactant can change Inter Facial Tension between oil and water allowing the irreducible oil to move together with water. There are three methods of using surfactant to recover the irreducible oil which are stimulation, Huff and Puff and Flooding.
Stimulation is a process to clean up pores surrounding wellbores. The surfactant is dissolved in oil to form surfactant solution. The solution is injected into wellbores and penetrates perforated zones to clean up cakes and scales attached to the perforation holes. The surfactant solution is soaked for few days to allow it reacts with cakes and scales. Surfactant used in the stimulation is generally oil dissolved surfactant. Cakes and scales formed by irreducible oil and debris are cleaned by the surfactant solution. Clean perforation holes allow more oil to flow into a wellbore.
Surfactant is chemical material which has ability to dissolve oil in water by forming emulsion. Without surfactant, oil is always separated from water and it’s impossible to dissolve. The irreducible oil in the reservoir is trapped and can’t be pushed by water as oil and water has high interfacial tension. Surfactant can change Inter Facial Tension between oil and water allowing the irreducible oil to move together with water. There are three methods of using surfactant to recover the irreducible oil which are stimulation, Huff and Puff and Flooding.
Stimulation is a process to clean up pores surrounding wellbores. The surfactant is dissolved in oil to form surfactant solution. The solution is injected into wellbores and penetrates perforated zones to clean up cakes and scales attached to the perforation holes. The surfactant solution is soaked for few days to allow it reacts with cakes and scales. Surfactant used in the stimulation is generally oil dissolved surfactant. Cakes and scales formed by irreducible oil and debris are cleaned by the surfactant solution. Clean perforation holes allow more oil to flow into a wellbore.
Huff and Puff is similar with Stimulation except Huff and Puff has deeper invasion. In the Huff and Puff method, surfactant solution could reach 10 meters away from well bore. The surfactant solution is soaked for 3 or 4 days and then the well is reopened to produce. The surfactant will flow back to the well carrying irreducible oil. In this method, production of neighboring wells could also increase because of some surfactant leaks to the well.
EOR method consists of producing and injection wells. Surfactant solution is injected into injection well and flows into the reservoir system. The surfactant solution with oil and water is recovered from producing wells. Each injection well has many producing wells to capture the response of the injection. Location of producing and injection wells is normally a radial pattern. The response of EOR injection takes much longer than well stimulation or Huff and Puff. However, EOR process is continuous so once the system is set up, we don’t need work over anymore.
General problems of surfactant injection are salinity and temperature. Surfactant will precipitate when it meets saline formation water. Higher salinity formation water will create more solids resulted from precipitation reaction. The particles produced could block pore spaces and plug the entire reservoir system and endanger the production. This danger makes surfactant injection was not popular until an improved performance surfactant which has salinity resistance performance is discovered. The other problem of surfactant is low operating temperature. The old surfactant has maximum operating temperature of only about 70 oC. The improved performance surfactant should has maximum operating temperature more than 200 oC. The surfactant for well injection has therefore salinity resistance and high operating temperature performances.
What is Biodiesel and How to Make it
The American Society for Testing and Materials (ASTM) defines biodiesel fuel as mono-alkyl esters of long chain fatty acids derived from a renewable lipid feedstock, such as vegetable oil or animal fat. Biodiesel is constructed from 2 words i.e.: “Bio” and “Diesel”. The word ‘‘Bio’’ represents renewable and biological source in contrast to petroleum-based diesel fuel. The word ‘‘Diesel’’ refers to its use in diesel engines. As an alternative fuel, biodiesel can be used in neat form or mixed with petroleum-based diesel.
Biodiesel, as an alternative fuel, has many positive benefits. It is derived from renewable and domestic resources. The use of biodiesel thereby relieving reliance on petroleum fuel which Indonesia are now importing it. Biodiesel is also biodegradable and non-toxic. Comparing with petroleum-based diesel, biodiesel has a more favourable combustion emission profile, such as low emissions of carbon monoxide, particulate matter and unburned hydrocarbons. Carbon dioxide produced by combustion of biodiesel can be recycled by photosynthesis, thereby minimizing the impact of biodiesel combustion on the greenhouse effect (Körbitz, 1999; Agarwal and Das, 2001).
Biodiesel has a relatively high flash point (150 °C), which makes it less volatile and safer to transport or handle than petroleum diesel (Krawczyk, 1996). It provides lubricating properties that can reduce engine wear and extend engine life (Von Wedel, 1999). In brief, these merits of biodiesel make it a good alternative to petroleum-based fuel and have led to its use in many countries, especially in environmentally sensitive areas.
The most common way to produce biodiesel is by transesterification, which refers to a catalyzed chemical reaction involving vegetable oil and alcohol to yield biodiesel or fatty acid methyl esters and glycerol. Triacylglycerols (triglycerides) as the main component of vegetable oil consist of three long chain fatty acids esterified to a glycerol backbone. When triacylglycerols react with methanol, the three fatty acid chains are released from the glycerol skeleton and combine with the alcohol to yield fatty acid alkyl esters (e.g., fatty acid methyl esters or FAME). Glycerol is produced as a by-product which can be utilized later as soap raw material. Methanol is the most commonly used alcohol because of its low cost and easy to find in general chemical stores.
The very first process before putting used cooking oil into the plant is to screen the oil to separate it from debris. The screened oil is mixed with methanol and steered for about 45 minutes at 55 oC in the mixing tank. The liquid is then settled for about 30 minutes to separate biodiesel from glycerol. Biodiesel produced still needs to be washed by water to dissolve impurities such as glycerol, soap, catalyst, methanol and other remained chemical materials. The washing water is then removed by boiling it for about 45 minutes.
Biodiesel, as an alternative fuel, has many positive benefits. It is derived from renewable and domestic resources. The use of biodiesel thereby relieving reliance on petroleum fuel which Indonesia are now importing it. Biodiesel is also biodegradable and non-toxic. Comparing with petroleum-based diesel, biodiesel has a more favourable combustion emission profile, such as low emissions of carbon monoxide, particulate matter and unburned hydrocarbons. Carbon dioxide produced by combustion of biodiesel can be recycled by photosynthesis, thereby minimizing the impact of biodiesel combustion on the greenhouse effect (Körbitz, 1999; Agarwal and Das, 2001).
Biodiesel has a relatively high flash point (150 °C), which makes it less volatile and safer to transport or handle than petroleum diesel (Krawczyk, 1996). It provides lubricating properties that can reduce engine wear and extend engine life (Von Wedel, 1999). In brief, these merits of biodiesel make it a good alternative to petroleum-based fuel and have led to its use in many countries, especially in environmentally sensitive areas.
The most common way to produce biodiesel is by transesterification, which refers to a catalyzed chemical reaction involving vegetable oil and alcohol to yield biodiesel or fatty acid methyl esters and glycerol. Triacylglycerols (triglycerides) as the main component of vegetable oil consist of three long chain fatty acids esterified to a glycerol backbone. When triacylglycerols react with methanol, the three fatty acid chains are released from the glycerol skeleton and combine with the alcohol to yield fatty acid alkyl esters (e.g., fatty acid methyl esters or FAME). Glycerol is produced as a by-product which can be utilized later as soap raw material. Methanol is the most commonly used alcohol because of its low cost and easy to find in general chemical stores.
The very first process before putting used cooking oil into the plant is to screen the oil to separate it from debris. The screened oil is mixed with methanol and steered for about 45 minutes at 55 oC in the mixing tank. The liquid is then settled for about 30 minutes to separate biodiesel from glycerol. Biodiesel produced still needs to be washed by water to dissolve impurities such as glycerol, soap, catalyst, methanol and other remained chemical materials. The washing water is then removed by boiling it for about 45 minutes.
Saturday, August 9, 2008
New Business of Biodiesel from Waste Cooking Oil
The world in peril caused by global warming has drawn international attention. Weather changes and sinking islands experienced by millions people indicated strong alerts for human life. On the other side the rise of fuel price soaring to more than US$ 100 shows that the petroleum resources are getting scarce. Both phenomena inspire me to write this article.
Linking up renewable energy with sustainable development is crucial. However, many renewable energy technologies are very expensive, high tech, and fabricated by and for the affluent population. Biodiesel, in contrast, is one of the few renewable energy technologies that transcend such pitfalls; it is low-tech, viable for local production, easy to use, and in Indonesia and other tropical regions it is economically competitive. Biodiesel is not only renewable source of energy but also produces much less pollution.
Biodiesel has potential to stimulate growth in multiple sectors of the economy. Biodiesel can create both industrial and agricultural economic opportunities. Furthermore, biodiesel does not require a new infrastructure. The existing infrastructure for petroleum diesel fuel is just perfect and is therefore highly practical. Biodiesel should therefore be considered seriously as an important tool for sustainable development.
High cost of biodiesel is the only major current obstacle to its commercialization. Biodiesel usually costs over US$ 1/l, compared to US$0.8/l for petroleum-based diesel. It is reported that the high cost of biodiesel is mainly due to the cost of virgin vegetable oil (Krawczyk, 1996; Connemann and Fischer, 1998). For example, in Indonesia, palm oil is sold on average for about $0.85/l in November 2007. Therefore, it is not surprising that biodiesel produced from pure palm oil costs much more than petroleum-based diesel. Exploring ways to reduce the high cost of biodiesel is of much interest in recent biodiesel research, especially for those methods concentrating on minimizing the raw material cost. The use of used cooking oil instead of virgin oil to produce biodiesel is an effective way to reduce the raw material cost because it is estimated to be about half the price of virgin oil (Supple et al., 1999). In addition, using used cooking oil could also help to solve the problem of used oil disposal (Wiltsee, 1998).
We have initiated to construct a simple machine or reactor to process the used or waste cooking oil to biodiesel in our City, Bogor, West Java, Indonesia. Our machine maximum capacity is only about 1 ton per day. The cost to make the simple machine was only about US$ 15,000. We then developed and improved the machine material cooperating with Surfactant and Bioenergy Research Centre (SBRC-IPB) as shown in the picture. Our biodiesel is used to fuel our operation cars which are a new Innova Kijang 2008 and old High Line Daihatsu. We have been using bioidesel for almost 2 years for the old car fuel. Our bioidiesel is also used to fuel city bus in our city, called Transpakuan. The cetane number of our bioidiesel is more than 60 so we call our biodiesel is BiSel 60.
Due to big demand on the biodiesel, we are looking for more used or waste cooking oil suppliers from all over the world. This business is expanding well and more bigger machines will be built in the future. You all can contact my email or comment this Blog if you are interested.
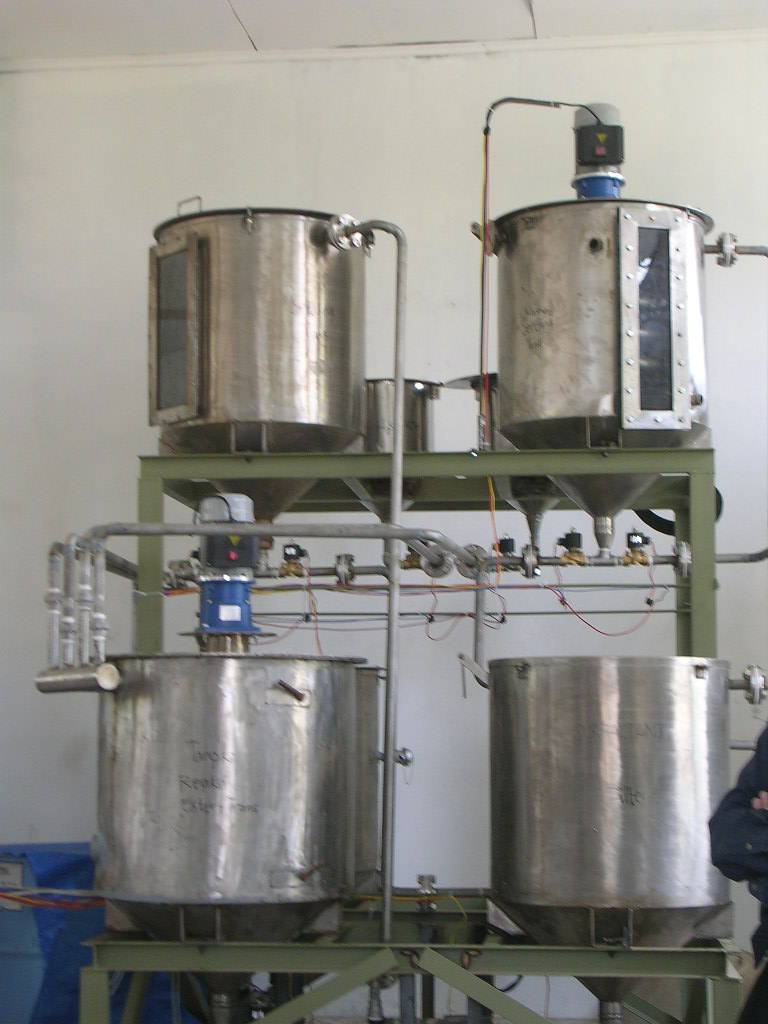
Linking up renewable energy with sustainable development is crucial. However, many renewable energy technologies are very expensive, high tech, and fabricated by and for the affluent population. Biodiesel, in contrast, is one of the few renewable energy technologies that transcend such pitfalls; it is low-tech, viable for local production, easy to use, and in Indonesia and other tropical regions it is economically competitive. Biodiesel is not only renewable source of energy but also produces much less pollution.
Biodiesel has potential to stimulate growth in multiple sectors of the economy. Biodiesel can create both industrial and agricultural economic opportunities. Furthermore, biodiesel does not require a new infrastructure. The existing infrastructure for petroleum diesel fuel is just perfect and is therefore highly practical. Biodiesel should therefore be considered seriously as an important tool for sustainable development.
High cost of biodiesel is the only major current obstacle to its commercialization. Biodiesel usually costs over US$ 1/l, compared to US$0.8/l for petroleum-based diesel. It is reported that the high cost of biodiesel is mainly due to the cost of virgin vegetable oil (Krawczyk, 1996; Connemann and Fischer, 1998). For example, in Indonesia, palm oil is sold on average for about $0.85/l in November 2007. Therefore, it is not surprising that biodiesel produced from pure palm oil costs much more than petroleum-based diesel. Exploring ways to reduce the high cost of biodiesel is of much interest in recent biodiesel research, especially for those methods concentrating on minimizing the raw material cost. The use of used cooking oil instead of virgin oil to produce biodiesel is an effective way to reduce the raw material cost because it is estimated to be about half the price of virgin oil (Supple et al., 1999). In addition, using used cooking oil could also help to solve the problem of used oil disposal (Wiltsee, 1998).
We have initiated to construct a simple machine or reactor to process the used or waste cooking oil to biodiesel in our City, Bogor, West Java, Indonesia. Our machine maximum capacity is only about 1 ton per day. The cost to make the simple machine was only about US$ 15,000. We then developed and improved the machine material cooperating with Surfactant and Bioenergy Research Centre (SBRC-IPB) as shown in the picture. Our biodiesel is used to fuel our operation cars which are a new Innova Kijang 2008 and old High Line Daihatsu. We have been using bioidesel for almost 2 years for the old car fuel. Our bioidiesel is also used to fuel city bus in our city, called Transpakuan. The cetane number of our bioidiesel is more than 60 so we call our biodiesel is BiSel 60.
Due to big demand on the biodiesel, we are looking for more used or waste cooking oil suppliers from all over the world. This business is expanding well and more bigger machines will be built in the future. You all can contact my email or comment this Blog if you are interested.
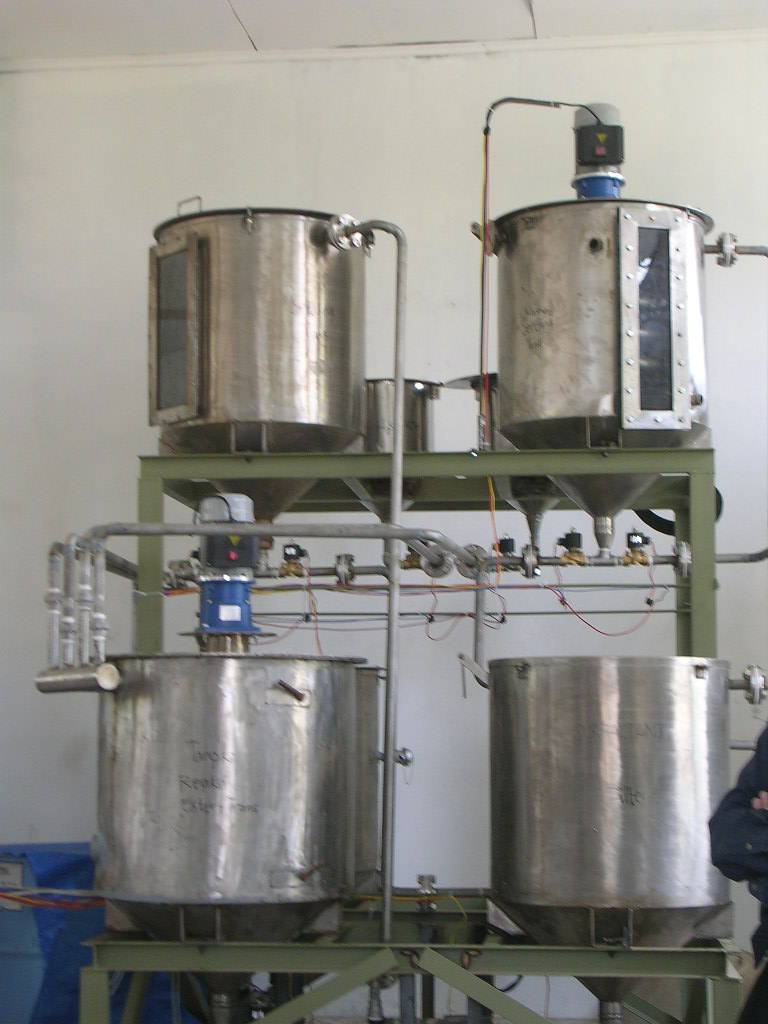
Subscribe to:
Posts (Atom)